As the global demand for renewable energy continues to grow, the photovoltaic industry is developing rapidly and becoming an important part of the future energy structure. In the manufacturing process of photovoltaic modules, the demand for processing precision metal parts is increasing, and customized CNC (computer numerical control) processing technology provides strong support for the photovoltaic industry with its high precision, high efficiency and flexibility. This article will explore the application of customized CNC machining in the photovoltaic industry and how it can improve production efficiency, reduce costs and improve the overall performance of photovoltaic modules.
1. The Importance of CNC Machining in the Photovoltaic Industry
The manufacturing of photovoltaic modules involves multiple key components, such as aluminum alloy frames, conductive busbars, inverter radiators, bracket systems, etc. The processing accuracy of these components directly affects the performance and stability of the photovoltaic system. CNC machining technology can control precision machine tools through computers to perform high-precision cutting, drilling, milling and engraving of metal materials to ensure stable product quality.
The important role of customized CNC machining in the photovoltaic industry is reflected in the following aspects:
High-precision manufacturing: ensure the accurate size of key parts of photovoltaic modules, reduce assembly errors, and improve system reliability.
High-efficiency production: CNC machine tools can realize automated processing, improve production efficiency, and meet the needs of large-scale photovoltaic production.
Diversified processing capabilities: Support the manufacturing of complex parts of different materials (aluminum alloy, stainless steel, copper, etc.), which can meet the design needs of personalized photovoltaic modules.
2. Core applications of customized CNC processing
(1) High-precision processing of photovoltaic aluminum alloy frames
The aluminum alloy frames of photovoltaic modules need to have high strength, corrosion resistance and good assembly properties to ensure that solar panels can operate stably and long-term in harsh outdoor environments. The advantages of customized CNC processing in frame manufacturing include:
High-precision cutting and drilling: Ensure the accuracy of frame connection parts and improve the assembly efficiency of photovoltaic modules.
Automated milling and surface treatment: Use CNC milling machines to process frame chamfers and embed grooves to optimize the appearance and structural stability of modules.
(2) Customized processing of photovoltaic inverter heat sinks
The photovoltaic inverter is the core component of the solar energy system, responsible for converting direct current into alternating current. Its heat dissipation performance directly affects the conversion efficiency and service life. CNC machining can achieve:
High-efficiency heat sink machining: CNC equipment can accurately machine multi-layer fin structures to improve heat dissipation and ensure long-term stable operation of the inverter.
Customization of high thermal conductivity materials: Accurately process high thermal conductivity materials such as copper and aluminum alloys to optimize heat conduction and improve energy efficiency.
(3) Processing of solar brackets and tracking system components
Photovoltaic bracket systems are used to fix solar panels and adjust their angles to optimize the absorption rate of sunlight. The application of CNC machining in bracket manufacturing includes:
High-strength connector machining: Ensure the stability of the bracket under different climatic conditions.
Customized parts production: CNC machining can quickly produce personalized customized brackets according to different terrains and installation requirements.
(4) CNC machining of photovoltaic cell production equipment
Photovoltaic cell production equipment (such as screen printing machines, laser dicing machines, laminating machines, etc.) requires a large number of precision metal parts. CNC machining can provide high-precision mechanical parts to ensure long-term stable operation of the equipment and improve the production quality of photovoltaic cells.
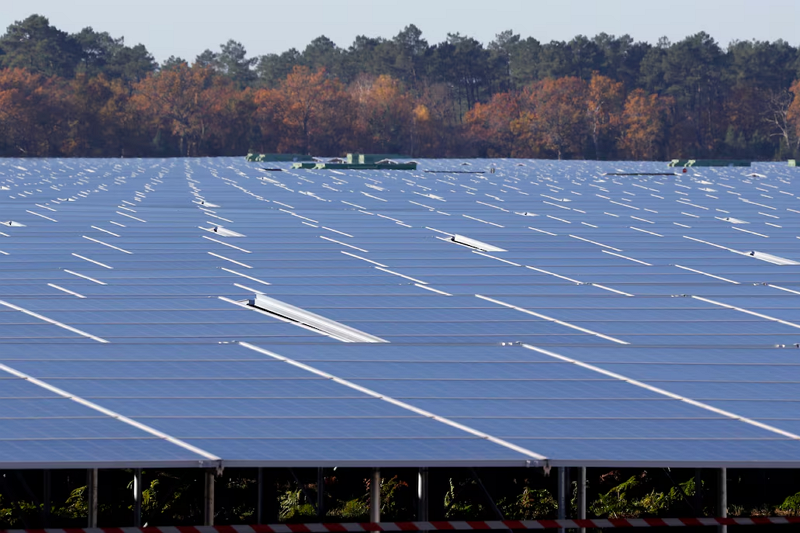
3. How CNC machining can improve the sustainable development of the photovoltaic industry
The sustainable development of the photovoltaic industry not only focuses on the efficiency of photovoltaic power generation, but also requires reducing energy consumption and resource waste during the production process. Customized CNC machining helps green manufacturing in the following aspects:
(1) Reduce material waste
CNC machining effectively reduces material waste and improves material utilization through precise cutting and optimized programming. For example, in the processing of aluminum alloy frames, optimizing tool paths can minimize waste and improve production efficiency.
(2) Energy-saving processing technology
Modern CNC machine tools use efficient and energy-saving drive systems to reduce power consumption, while optimizing processing parameters to reduce carbon emissions during the production process.
(3) Improve the life of photovoltaic modules
High-precision CNC machining ensures the quality of photovoltaic module parts, reduces failure rates, and extends service life, thereby reducing maintenance costs and improving overall energy conversion efficiency.
4. Future development trends and innovations
As the photovoltaic industry continues to innovate, customized CNC machining is also constantly upgrading. Future development trends include:
Intelligent CNC machining: Combined with AI to optimize tool paths to improve processing accuracy and efficiency.
Five-axis CNC technology: more refined processing capabilities, suitable for complex photovoltaic module manufacturing.
Automation and robot collaboration: CNC processing combined with robot assembly to achieve full automation of photovoltaic production and improve production flexibility and stability.