Driven by the "dual carbon" goal, the photovoltaic industry is accelerating its development towards high efficiency, thin film and intelligent direction. As the core equipment of semiconductor-level precision manufacturing, computer numerical control (CNC) machining technology has become a key breakthrough in improving the production efficiency of photovoltaic cells through nano-level precision control, dynamic process optimization and intelligent production line collaboration. This article analyzes its mechanism of action from three dimensions: technical path, application scenario and industrial value.
1. Three core breakthroughs in precision machining
Nano-level silicon wafer cutting technology
Using a multi-wire cutting CNC system, the thickness of the silicon wafer is reduced from 180μm to below 130μm through the cooperation of 0.03mm ultra-fine diamond wire and high-precision servo feed system. The laser-assisted cutting technology developed by a Japanese equipment manufacturer, combined with CNC path planning, reduces the thickness of the cutting damage layer from 15μm to 5μm, and increases the material utilization rate by 22%.
Micro-groove precision etching process
In the preparation of TOPCon cells, the five-axis CNC etching equipment processes a nano-scale tunneling oxide layer with uniform depth on the back of the silicon wafer through rotating electrodes and three-dimensional trajectory control. Actual measured data show that this technology increases the cell conversion efficiency by 0.8-1.2 percentage points and the yield by 9%.
Printed electrode dynamic compensation system
For HJT cell silver paste printing, the CNC-driven micron-level jetting system combines visual feedback to adjust the nozzle pressure and movement speed in real time. After a leading enterprise applied it, the main grid line width was reduced from 80μm to 50μm, the paste consumption was reduced by 36%, and the electrode contact resistance decreased by 18%.
2. Full-process efficiency optimization system
Digital process chain collaboration
Build a CNC processing virtual model based on digital twin technology and complete process parameter optimization in the trial production stage. Through this technology, LONGi Green Energy has increased the mass production efficiency of PERC cells from 23.2% to 24.5%, and shortened the process development cycle by 40%.
Online detection closed-loop control
A CNC laser thickness gauge is integrated after the PECVD process to monitor the thickness of the anti-reflection film in real time. Data shows that this technology improves the uniformity of film thickness from ±8% to ±3%, and reduces the rework rate by 75%.
Intelligent production scheduling system
Connect CNC equipment to the production scheduling system through the industrial Internet platform to achieve dynamic matching of multi-process capacity. Trina Solar's pilot project shows that the overall equipment efficiency (OEE) has increased from 78% to 92%, and the single-shift capacity has increased by 28%.
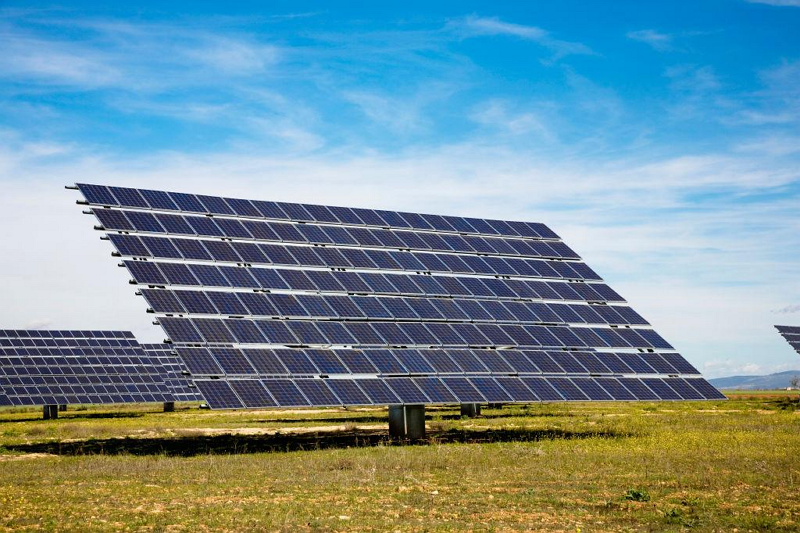
3. Typical application scenarios
Heterojunction battery TCO film preparation
Using CNC magnetron sputtering equipment, the TCO film square resistance uniformity reaches ±5% and the transmittance is increased to more than 92% through the optimization of the target material motion trajectory.
Laser scribing of shingled modules
The five-axis laser scribing machine combined with CNC path planning controls the defective rate of cracks within 0.1% and increases the scribing speed to 800mm/s.
Precision machining of component frames
The dual-spindle CNC machining center achieves ±0.05mm positioning accuracy of the frame slot, shortening the component packaging time by 40%.
4. Industry value and development trend
Improved economic efficiency
According to statistics, high-precision CNC technology reduces the unit cost of battery cells by 15-20%. A leading enterprise has reduced the investment in single GW production capacity by 120 million yuan through CNC transformation.
Technology evolution direction
Ultra-precision grinding: Develop CMP (chemical mechanical polishing) and CNC composite processing technology, and control the surface roughness Ra value within 0.5nm
Laser direct writing technology: Combine femtosecond laser and CNC scanning to achieve 1μm line width electrode printing
Adaptive processing system: Introduce AI algorithm to predict processing errors, dynamically adjust parameters to achieve closed-loop control
Green manufacturing empowerment
Through CNC optimization of the cutting fluid circulation system, the water consumption of a single silicon wafer is reduced from 1.2L to 0.5L, and the cost of industrial water is reduced by 60%.
Summary
As the efficiency of photovoltaic cells approaches the theoretical limit, high-precision CNC processing technology is transforming from a simple manufacturing tool to a core carrier of technological innovation. According to SEMI's forecast, the global photovoltaic-specific CNC equipment market will exceed US$5 billion by 2026, with a compound annual growth rate of 18%. In the future, with the industrialization of new technologies such as quantum dot printing and perovskite stacking, CNC processing will play a key role in nano-scale material manipulation, cross-scale structure manufacturing and other fields, and continue to promote the photovoltaic industry to leap towards higher efficiency and lower cost.